Autostradowa nawierzchnia betonowa o niskim śladzie węglowym
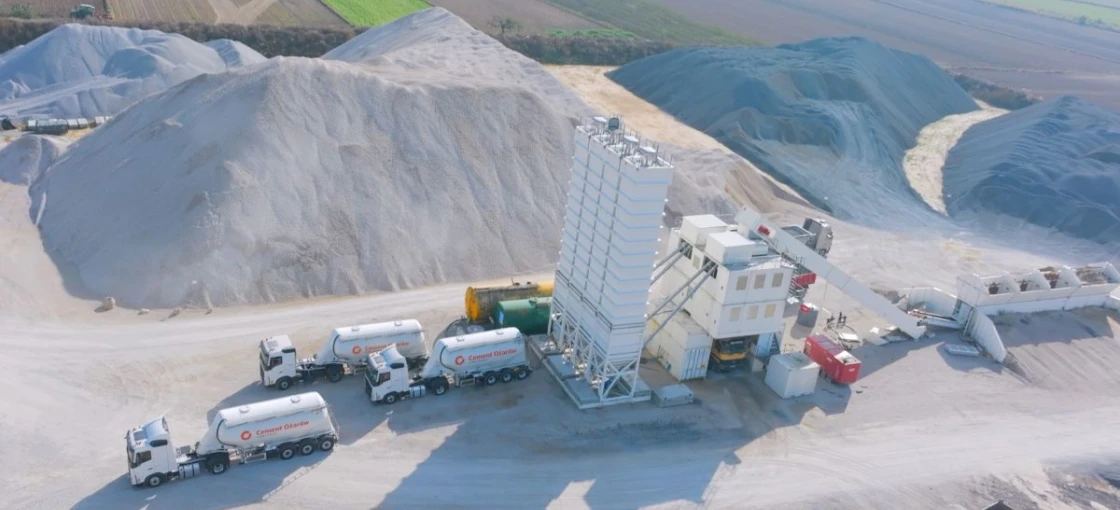
Beton jest drugim po wodzie najczęściej stosowanym materiałem na świecie. To nie jego emisyjność, a skala zastosowania powoduje, że dzisiaj odpowiada za 8-10% antropogenicznej emisji CO2, dlatego nawet najmniejsze podjęte działania przekładają się na duże liczby. Branża cementowo-betonowa podążą drogą do neutralności emisyjnej. Liczne działania podejmowane są w wielu obszarach, począwszy od działań na etapie produkcji klinkieru skończywszy na działaniach związanych z konstrukcją budowlaną i jej ewentualną rozbiórką czy recyklingiem, mające na celu obniżenie śladu węglowego w całym łańcuchu wartości.
Pierwsza nawierzchnia betonowa powstała w 1888 roku na placu Bluechera (obecnie Plac Solny) we Wrocławiu. Początki technologii nawierzchni betonowych rozpoczęły się w latach 30. XX wieku, kiedy to budowano autostradę A4, łączącą zagłębie Ruhry z zagłębiem górnośląskim.
Po II Wojnie Światowej nawierzchnie betonowe wykonywano głównie na drogach o znaczeniu strategicznym. W latach 1918-1939, budowano nawierzchnie dróg krajowych głównie z kostki kamiennej, kostki klinkierowej i betonu cementowego. Współczesne drogi betonowe w Polsce są wynikiem wieloletniego rozwoju i doświadczeń, które obejmują zarówno konstrukcję, jak i technologię wykonania nawierzchni betonowych. W 1995 roku wybudowano pierwszy odcinek autostrady o nawierzchni betonowej, co było współczesnym przełomem w historii polskich dróg betonowych.
Budowa dróg betonowych w Polsce jest wynikiem rozwoju technologii oraz wykorzystania doświadczeń europejskich i światowych.
W Polsce kierowcy mają do dyspozycji łącznie 5115,6 km dróg szybkiego ruchu w podziale 1849,2 km autostrad i 3266,4 km dróg ekspresowych. Z roku na rok przybywa dróg betonowych, zgodnie z statystykami na koniec 2023 r. było 1168,19 km dróg ekspresowych i autostrad z nawierzchnią betonową, co stanowi 22,8% sieci dróg szybkiego ruch w Polsce.
Według danych EUPAVE (Europejskie Stowarzyszenie Nawierzchni Betonowych) nawierzchnia betonowa była także na 45,4 km (0,16%) dróg wojewódzkich, 600 km (0,5%) dróg powiatowych i 1200 km (0,5%) dróg gminnych.
Natomiast w Europie nawierzchnie betonowe występują na autostradach w ilości – Austria > 50%, Belgia – około 40% i Niemcy > 50%, Wielka Brytania – około 50%, Czechy > 65%.
Drogi te mają liczne zalety, są tańsze i zdecydowanie trwalsze w porównaniu z nawierzchniami z mieszanek mineralno-asfaltowymi, nie występuje na nich efekt koleinowania i posiadają lepszą widoczność podczas jazdy z uwagi na ich jasny kolor.
Nawierzchnie betonowe w Polsce – wymagania
W Polsce dotychczas budowane drogi betonowe były układane na podbudowie z mieszanek związanych cementem o grubości około 18-20 cm, warstwa ta w zasadzie jest pierwszą betonową warstwą konstrukcji drogi ekspresowej. Następnie na podbudowie z mieszanki związanej cementem rozkłada się geowłókninę i dopiero wtedy przystępuje się do wykonania ostatniej warstwy czyli nawierzchni betonowej.
W ostatnich latach wykonano w naszym kraju również kilka dróg ekspresowych z konstrukcją z podbudowy zasadniczej z mieszanki niezwiązanej 0/31,5 grubości 27 cm zamiast warstwy chudego betonu i co za tym idzie grubszą warstwą betonu nawierzchniowego – 32cm. Wymagania dotyczące cementów obowiązuje na drogach szybkiego ruchu WWiORB D.05.03.04 V.02 Nawierzchnia z betonu cementowego (dokument wzorcowy)
Cementy do betonowych nawierzchni drogowych w kategoriach ruchu od KR5 do KR7, kategoria środowiska E3.
Doświadczenia krajowe dotyczące wyboru rodzaju cementu do nawierzchni betonowych koncentrowały się dotychczas na zastosowaniu cementu CEM I 42,5 R(N) spełniające dodatkowe właściwości specjalne zawarte w dokumentacji technicznej. W celu redukcji śladu węglowego oraz ograniczenia ryzyka wystąpienia reakcji alkalia-krzemionka, zastosowano cement CEM II/B-S 42,5 R-NA. JASNY CEM II/B-S 42,5 R-NA jest cementem portlandzkim żużlowym, o klasie wytrzymałości 42,5 i wysokiej wytrzymałości wczesnej (R) zgodny z normą PN-EN 197-1 oraz o niskiej zawartości alkaliów według PN-B-19707. Cement przeznaczony jest do specjalistycznych zastosowań w tym do infrastruktury drogowo-mostowej. Składnik główny nieklinkierowy występujący w tym cemencie, którym jest mielony granulowany żużel wielkopiecowy ma kluczowy wpływ na ograniczenie wystąpienia reakcji alkalia-kruszywo. Rola granulowanego żużla wielkopiecowego została potwierdzona w badaniach określenia wpływu zawartości alkaliów całkowitych, rozpuszczalnych oraz aktywnych w cemencie na reakcje z kruszywem silnie reaktywnym ze szkła borowo-krzemionkowego zgodnie z ASTM. Badania potwierdziły że cement CEM II/B-S 42,5 R-NA hamuje reakcję i pozwala zakwalifikować cement jako niewywołujący reakcji alkalia-krzemionka, w stosunku do kruszyw na nią podatnych.
Dodatkowo elementy wykonane na cemencie JASNY CEM II/B-S 42,5 R-NA mają jaśniejszy kolor, co przyczynia się do wielu pozytywnych aspektów. Z perspektywy nawierzchni betonowych można wymienić m.in.: przeciwdziałanie globalnemu ociepleniu, redukcja efektu miejskiej wyspy ciepła, oszczędność kosztów i energii na oświetlenie dróg, poprawa widoczności, szczególnie w trudnych warunkach atmosferycznych co jest kluczowe dla bezpieczeństwa drogowego.
Przez zastosowanie mielonego granulowanego żużla wielkopiecowego również ograniczony jest ślad węglowy cementu JASNY CEM II/B-S 42,5 R-NA, który jest niższy o ~30% względem CEM I 42,5 R. Ta wartość przekłada się w znaczącym stopniu na obniżenie śladu węglowego nawierzchni betonowych.
Wykonano szereg testów pozwalających potwierdzić przydatność cementu CEM II/B-S 42,5 R-NA o niskim śladzie węglowym w nawierzchniach betonowych. Dla zaprojektowanych receptur oszacowano ślad węglowy betonu CO2eq w obrębie fazy A1-A3 zgodnie z oceną cyklu życia LCA (Life Cycle Assessment) PN-EN 15804+A2:2020-04. Ocena cyklu życia obejmuje kilka faz co przedstawiono w poniższej tabeli. Do wyliczeń śladu węglowego betonu [kg CO2eq/m3 mieszanki betonowej) uwzględniono produkcję komponentów, ich transport do miejsca wbudowania oraz wytworzenie 1 m3 betonu.
W tradycyjnym i powszechnie stosowanym rozwiązaniu, cement odpowiedzialny jest za około 84% śladu węglowego betonu w fazie wyrobu A1-A3 (przyjęto wartość śladu węglowego dla CEM I 42,5 R (N) podaną w Deklaracji Środowiskowej III Typu opublikowaną przez Stowarzyszenie Producentów Cementu).
Wartości nieznacznie się różnią w zależności od warstwy betonu: górna czy dolna.
Na skutek wykorzystania cementu o obniżonym śladzie węglowym CEM II/B-S 42,5 R-NA w miejsce cementu CEM I 42,5 R (N), proporcje udziału poszczególnych składowych uległy zmianie.
W tym rozwiązaniu cement jest odpowiedzialny za około 77% śladu węglowego betonu w fazie wyrobu A1-A3. Wartość śladu węglowego dla CEM II/B-S 42,5 R-NA przyjęto zgodnie z Deklaracją Środowiskową III Typu Cement Ożarów.
W tabeli przedstawiono ślad węglowy betonu [kg CO2eq/m3] dla fazy wyrobu A1-A3 w zależności od warstwy nawierzchni oraz wykorzystanego cementu w przeliczeniu na wyprodukowanie 1m3 betonu.
Na przedstawionym odcinku A2 Siedlce Południe (dawniej Swoboda) – Malinowice (odcinek VI) powstanie 360 000 m2 nawierzchni wykonanej w technologii betonowej. Grubość górnej warstwy betonu GWB wynosi 5 cm, dolnej warstwy DWB 22 cm. Na podstawie tych danych wyliczono ilości do wyprodukowania betonu obu warstw: GWB – 18 000 m3 zaś DWB – 79 200 m3. Na skutek zmiany cementu CEM I 42,5 R(N) na cement CEM II/B-S 42,5 R-NA Cement Ożarów S.A. dla fazy wyrobu [A1-A3] zredukowano ślad węglowy betonu o 9 816 120 kg CO2eq, czyli ~30% względem tradycyjnego rozwiązania.
Państwa Europy Zachodniej poszły o krok dalej w ograniczeniu śladu węglowego nawierzchni betonowych, ponieważ w ich specyfikacjach technicznych nie ma zapisu, że do betonu dolnej i górnej warstwy należy stosować ten sam rodzaj i klasę cementu. W ostatnich latach na większości dróg budowanych w Niemczech normą stało się rozwiązanie opierające się na wykorzystywaniu do dolnej warstwy cementu CEM III/A 42,5 N-LH/HSR/NA natomiast do górnej CEM I 42,5 R(N) – co zgodnie z polskimi przepisami jest niedopuszczalne. Należy sobie zadać pytanie czy to ograniczenie jest zasadne?
Ślad węglowy 1 m3 betonu dolnej warstwy w fazie wyrobu [A1-A3] na bazie cementu CEM III/A 42,5 N-LH/HSR/NA wynosi 186,6 [kg CO2eq/m3] (Wartości śladu węglowego cementu zgodnie z Deklaracją Środowiskową III Typu Cement Ożarów). Układ w śladzie węglowym poszczególnych składowych dla warstwy DWB przedstawia poniższy diagram.
Porównując wcześniejsze wyliczenia rozwiązań z zastosowaniem cementów CEM I 42,5 R(N) i CEM II/B-S 42,5 R-NA Cement Ożarów dla deklarowanego wbudowanego betonu nawierzchniowego na przedmiotowym kontrakcie do rozwiązania stosowanego w Europie Zachodniej (GWB – CEM I 42,5 R(N) oraz DWB – CEM III/A 42,5 N-LH/HSR/NA Cement Ożarów) można wykazać dodatkowe ograniczenie emisyjności. W porównaniu do CEM I 42,5 R(N) dla fazy wyrobu [A1-A3] możliwe jest zredukowanie śladu węglowego betonu o 11 460 240 kg CO2eq, czyli ~35%, natomiast względem CEM II/B-S 42,5 R-NA ta różnica jest mniejsza i wynosi 1 644 120 kg CO2eq, czyli ~7%.
STRABAG wspólnie z CEMENT OŻARÓW wprowadził rozwiązanie pozwalające znacznie zredukować ślad węglowy nawierzchni betonowej, co w dużym stopniu wpływa pozytywnie na środowisko, w którym żyjemy i pracujemy. Dodatkowo wspólna koncentracja nad dalszymi działaniami pozwoli na jeszcze większą redukcję. Cement Ożarów jako producent cementu CEM II/B-S 42,5 R-NA i Strabag jako producent betonu i wykonawca nawierzchni betonowej przez wspólną determinację i strategię, kreują oraz wdrażają nowe rozwiązania przy wykonywaniu nowoczesnych, trwałych nawierzchni betonowych o niskim śladzie węglowym.
- Krzysztof Zadrożny, Dyrekcja Autostrad i Dużych Projektów PE w STRABAG Sp. z o.o.
- Piotr Molenda, Dział Doradztwa Technicznego i Rozwoju w Cement Ożarów S.A.
- Artur Paszkowski, Dział Doradztwa Technicznego i Rozwoju w Cement Ożarów S.A.
- Krzysztof Pytel, Segment Infrastruktura w Cement Ożarów S.A.
Zobacz także Prezentację Cement Ożarów w portalu.