Technologia produkcji podkładów kolejowych strunobetonowych
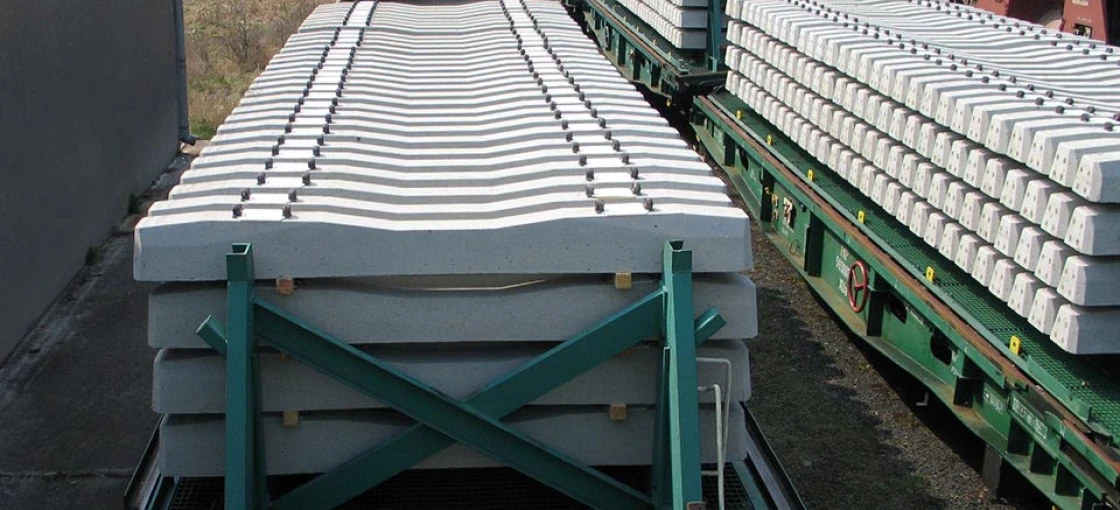
Etapy produkcji podkładów strunobetonowych
Wytworzenie podkładów strunobetonowych składa się z kilku etapów. Będą to:
Przygotowanie formy i zbrojenia
Używa się stalowych form wielokomorowych (najczęściej o długości 100–200 m). W formach napina się stalowe liny lub druty sprężające (tzw. struny), zazwyczaj o wytrzymałości ≥ 1 570 MPa. Struny są napinane na sucho przed zalaniem mieszanką betonową (technologia „pre-tensioning”).
Zalewanie form betonem
Zazwyczaj używa się betonu klasy C50/60 lub wyższej, często samozagęszczalnego (SCC). Beton musi charakteryzować się wysoką wytrzymałością wczesną (po 12–24 h), aby możliwe było szybkie sprężenie i rozformowanie. Mieszanka musi spełniać wymagania mrozoodporności, nasiąkliwości i odporności chemicznej.
Dojrzewanie i pielęgnacja betonu
Beton dojrzewa w formach, często w warunkach podwyższonej temperatury (parowanie, nagrzewanie form). Czas dojrzewania wynosi zazwyczaj 12–24 godziny, po czym beton osiąga wytrzymałość potrzebną do przeniesienia sił sprężających.
Sprężenie i cięcie elementów
Po uzyskaniu odpowiedniej wytrzymałości sprężone struny są odcinane (następuje ich rozprężenie), co przenosi siły sprężające na beton. Następnie podkłady są cięte na odpowiednią długość (najczęściej 2,4–2,6 m dla torów normalnych).
Obróbka wykończeniowa
Montowane są wkładki pod przytwierdzenia szyn (np. systemy typu Pandrol, Vossloh). Podkłady poddaje się szlifowaniu, numerowaniu i impregnacji (jeśli wymagane).
Kontrola jakości
Każda partia podkładów przechodzi badania wytrzymałościowe, geometryczne i materiałowe. Kontrola obejmuje m.in.: próby zginania, badanie wytrzymałości betonu, przylegania drutów, nasiąkliwości, mrozoodporności i trwałości zamocowań.
Wymagania techniczne dla podkładów strunobetonowych
Podkłady muszą spełniać normy krajowe i europejskie, m.in.:
- PN-EN 13230-2 – Podkłady i belki strunobetonowe do torów kolejowych
- PKP PLK – katalogi typów i WTWiORB (Warunki Techniczne Wykonania i Odbioru Robót).
Wybrane wymagania:
Klasa betonu - min. C50/60
Wytrzymałość na zginanie - ≥ 10 kN (w zależności od typu)
Odporność na mróz - min. F150 (150 cykli)
Nasiąkliwość - ≤ 5%
Masa podkładu - ok. 250–300 kg
Odchyłki wymiarowe - ±2 mm dla kluczowych wymiarów
Trwałość przytwierdzeń szyn - min. 2,5 kN (siła zakotwienia)
Systemy produkcji
Podkłady strunobetonowe powstają w następujących systemach produkcji:
Linia stacjonarna (ciągła forma) - najczęściej stosowana, gwarantująca wysoką wydajność (do 400 podkładów/dzień) oraz wysoką powtarzalność i automatyzację (robotyzacja dozowania, montażu wkładek, szlifowania).
Linia karuzelowa - rzadziej stosowana (bardziej popularna przy mniejszych seriach prefabrykatów), umożliwia elastyczną produkcję różnych typów podkładów.
Zalety podkładów strunobetonowych
Zastosowanie podkładów strunobetonowych daje szereg wymiernych korzyści. Są to:
- wysoka trwałość (nawet > 50 lat eksploatacji)
- odporność na warunki atmosferyczne i obciążenia dynamiczne
- powtarzalność i jakość przemysłowej produkcji
- możliwość zastosowania w torach klasy UIC 60, S49, także na łukach i w torach dużych prędkości.
Zastosowania podkładów strunobetonowych
Typowe miejsca, gdzie zastosowanie mają podkłady strunobetonowe, to:
- tory główne, stacyjne, bocznicowe
- linie kolejowe konwencjonalne i dużych prędkości (z odpowiednimi modyfikacjami)
- linie tramwajowe, metro, kolej aglomeracyjna (w wersjach specjalnych).
Fot. wps-sa.com.pl
Treści powiązane
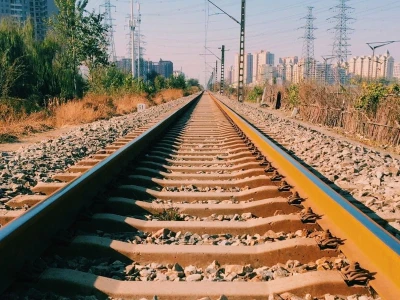
Problemy firm z branży budownictwa kolejowego
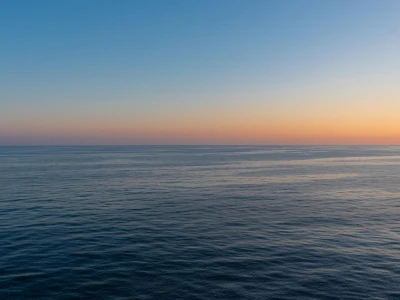
Najdłuższy tunel kolejowy na świecie
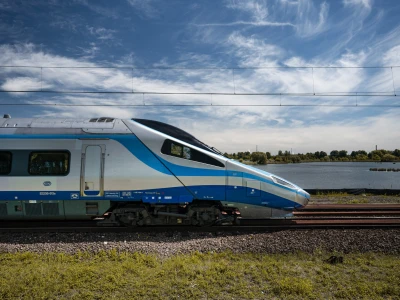
Inwestycje kolejowe 2025
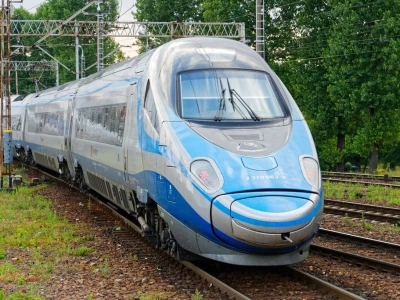
Krajowy Program Kolejowy
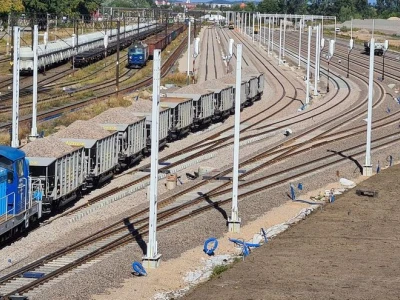
Zielone światło dla budownictwa kolejowego?
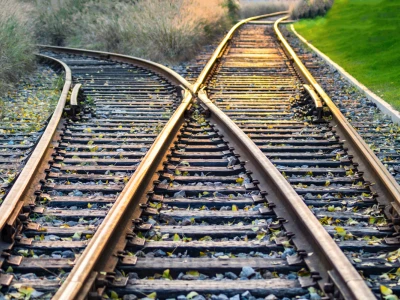