Planowanie produkcji oraz proces produkcji - komentuje Jacek "Prefabrykator" Trzcieliński
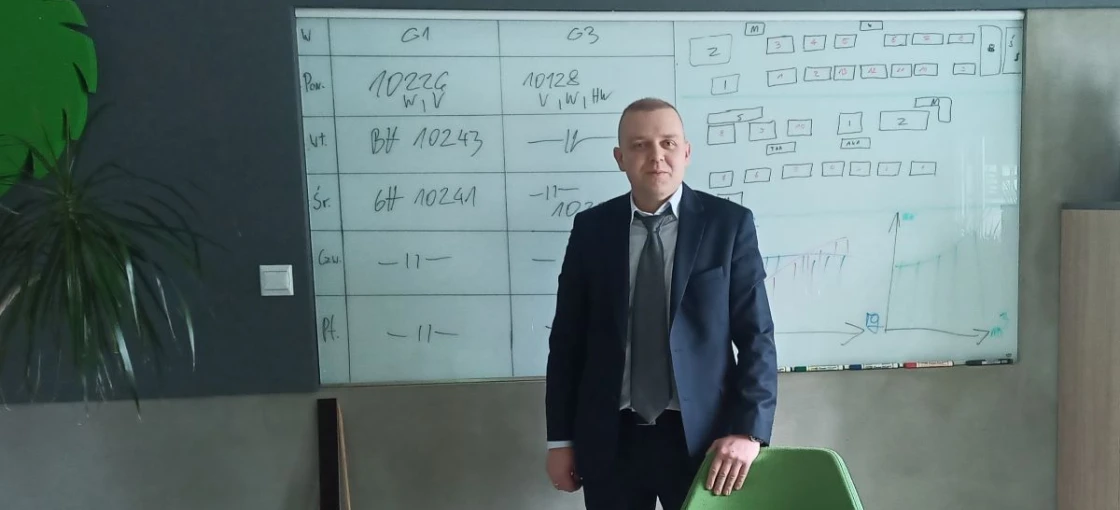
Rozpoczęcie procesu wytwórczego zaczyna się w momencie kontaktu Działu Handlowego z potencjalnym Klientem. Istotną rolę odgrywa tutaj system ERP (Enterprise Resource Planning) jak SAP, w skład którego wchodzą moduły, m.in. Działu Handlowego CRM (Customer Relationship Management). Przedstawiciel handlowy zakładu prefabrykacji nawiązując relację z Klientem musi skonsultować możliwości produkcyjne oraz cenowe z odpowiednią jednostką organizacyjną zakładu produkcji.
Szczegółowe planowanie produkcji następuje po otrzymaniu dokumentacji warsztatowej. Jednakże zanim do tego dojdzie, fabryka musi określić swoje możliwości produkcyjne, które wynikają z konkretnych zasobów jakimi dysponuje, a składają się na nie zasoby ludzkie, technologiczne, ziemskie, jak i kapitałowe:
- Wydajność węzła betoniarskiego (istotne, gdy fabryka sprzedaje również beton towarowy lub wytwarza beton na wiele linii technologicznych, w tym elementy wymagające dużej ilości betonu, jak np. stopo-słupy i dźwigary hal produkcyjno-magazynowych)
- Logistyka dystrybucji betonu na poszczególne stanowiska produkcyjne
- Ilość oraz parametry techniczne stanowisk produkcyjnych
- Technologia i logistyka procesu produkcji (np. magazyn, karuzela, dojrzewalnia), możliwości gniazd produkcyjnych wytwarzające pół-produkty
- Zasoby ludzkie
- Wielkość placów składowych na terenie fabryki. W szczególnych przypadkach (np. budownictwo infrastrukturalne) może okazać się opłacalne stworzenia placów składowych na terenie budowy
- Możliwość gromadzenia zapasów magazynowych surowców i komponentów oraz płynności finansowej przedsiębiorstwa.
Poszczególne parametry ocenia się wskaźnikowo, natomiast szczegółowe planowanie produkcji polega na symbiotycznym połączeniu poszczególnych parametrów ze sobą oraz z rzeczywistymi elementami zleconymi do produkcji. Szczególną rolę odgrywa „deadline” w postaci terminów załadunków na poszczególne środki transportu. Szukanie optymalnego rozwiązania polega na iteracyjnym rozwiązaniu równań o wielu parametrach i danych wejściowych. Niestety znajdując nawet optimum napotykamy wiele problemów życia codziennego, jak chociażby absencje pracowników na konkretnych kluczowych stanowiskach produkcyjnych, czy przestoje wynikłe z nagromadzenia prac w poszczególnych gniazdach produkcyjnych. Praca ta jest ciągła, a przez to poszukiwanie optymalnego rozwiązania niemal zawsze jest związane z niekończącymi się poprawkami. Zagadnienie to przypomina nieco słynny efekt motyla, czyli anegdotyczny opis problematyki układów równań różniczkowych Lorenza związanych z prognozowaniem pogody. Zmiana jednego z parametrów wejściowych nawet w niewielkim stopniu może spowodować duży wpływ na wynik końcowy. Ujmując rzecz obrazowo:
- Wpływ braku odpowiedniego surowca na magazynie jest prosty do zrozumienia, np. brak cementu w silosie lub dedykowanej szafki rozdzielczej do zatopienia w prefabrykowanej ścianie spowoduje niemożność wyprodukowania danych elementów.
- Jednak np. absencja jednego cieśli szalunkowego może (lecz nie musi) spowodować brak możliwości wykonania elementu na czas. Wszakże cieśli jest wielu, więc zwiększając tempo prac lub wykonując pracę w nadgodzinach teoretycznie mogliby zastąpić nieobecnego. Proza życia pokazuje, iż w praktyce nie zawsze jest to takie łatwe. Przy pełnym obłożeniu pracą nie są w stanie wykonać dodatkowych zadań, a przynajmniej nie bez odbicia się na jakości. Pracownicy nie są tożsami pod kątem umiejętności, więc nie można ich dowolnie wymieniać „sztuka za sztukę” niczym w pierwszym pełnometrażowym filmie Władysława Pasikowskiego.
Nade wszystko czynności muszą być wykonane w odpowiedniej kolejności gdyż one determinują możliwość rozpoczęcia kolejnych czynności prostych składających się na całość procesu.
Problematyka zasobów ludzkich oraz surowcowych czy magazynowych jest nadzorowana przy udziale systemu ERP oraz MES lub… arkuszy kalkulacyjnych, a niekiedy o zgrozo przy pomocy metody „pen and paper”. Na rynku dostępnych jest wiele systemów, jednakże wszystkie posiadają wady i zalety. Najpopularniejsze z nich dostosowane są do wielu branż przemysłowych, przez co posiadają duże uproszczenia, które nadają się do produkcji seryjnej (np. bloczki betonowe, pustaki stropowe, itd.) lecz kompletnie dyskwalifikuje je przy kompleksowej prefabrykacji budowlanej. Przeznaczone są do branży produkcyjnej, gdzie odbywa się produkcja seryjna o skończonej ilości rodzajów i typów, np. odlewy plastikowe, kształtki styropianowe, a nawet elementy bardziej złożone, ale produkowane seryjnie partiami, jak telewizory. W kompleksowej prefabrykacji obiektów budowlanych ilość i rodzaj elementów jest nieograniczony. W ramach jednego projektu może wystąpić przeszło tysiąc różnych elementów, podczas gdy fabryka produkuje kilka projektów jednocześnie.
Drugą możliwością są systemy dedykowane do branży prefabrykacji, które zawierają szereg narzędzi pomocnych przy zarządzaniu produkcją. Ich wadą jest to, iż wymuszają wprowadzanie konkretnych danych wejściowych, co (wbrew zapewnieniom dostawców tychże rozwiązań IT) wymusza, aby dokumentacja projektowa oparta była również na bazie oprogramowania tej samej marki. Dynamiczny, a zatem i elastyczny zakład prefabrykacji nie jest w stanie opierać się tylko na dokumentacji wykonywanej za pomocą jednego programu. Nawet jeżeli w skład danego zakładu prefabrykacji wchodzi wewnętrzne biuro projektowe, to nie jest też uzasadnionym przerabianie wszelkiej otrzymanej dokumentacji na „wewnętrzną”. Takie czynności mogą się zdarzyć sporadycznie, przy mniejszych objętościowo projektach.
Trzecią, najbardziej pracochłonną metodą jest opracowanie autorskiego systemu. Jako że jestem aktywny zawodowo, a ów artykuł przeczyta szereg przedstawicieli konkurencji, to pozwolę sobie pozostać przy ww. ogólnikach zachowując dla siebie wieloletnie know-how.
Jak wspomniałem wyżej – ścisła współpraca podmiotów realizujących przedsięwzięcie budowlane od samego początku jest kluczowa. Project Manager z ramienia Inwestora musi określić ramowo szacowany czas realizacji dokumentacji oraz dostaw, aby Zakład Produkcji sprawdził możliwości produkcyjne w zadanym czasookresie.
Sama dokumentacja oraz jej przepływ winien być administrowany należycie. Przy większych projektach dobrze jak zajmuje się tym osobna osoba koordynująca poszczególne branże, a pomocne w tym są platformy co-workingowe oparte na „chmurach”, np. Byggnet, Apricon, Dalux itd. gdyż materiały tam zamieszczone stanowią wiążącą umownie dokumentację. System samoistnie nadaje plikom kolejne wersje, daty, itd. dzięki czemu znacznie łatwiej jest odnaleźć się poszczególnym projektantom i wykonawcom. Maile, wygasłe linki do „serwera”, itd. odchodzą w niebyt. Cała dokumentacja projektowa znajduje się w jednym miejscu.
Dobrą regułą jest ustandaryzowanie dokumentacji pod kątem typizacji nazewnictwa oraz podziału dokumentacji pod kątem jakościowym. Znamienicie wpływa to na przejrzystość prac projektowych oraz praktycznego korzystania z opracowanej dokumentacji.
Każda z branż posiada symbole (np. A od architektura, czy K-konstrukcja) rozpoczynające nazwę rysunku. Następne symbole i liczby określają typ rysunku (rzut, przekroje, detale, etc.) nr budynku, piętra, itd.
Przystępując do procesu projektowego od samego początku inwestycji każda z branż uczestniczy w jej tworzeniu od samego początku, przez co kolejne wersje stanowią jej uszczegółowienie oraz oficjalnie zatwierdzony etap, która związana jest z konkretnymi sankcjami prawnymi. Dla przykładu większość wykonawców wg szwedzkiej nomenklatury uczestniczy w etapach:
- PH – preliminärhandlingar – dokumentacja koncepcyjna
- GH – granskningshandlingar – dokumentacja recenzowana wzajemnie przez branżystów
- BH – bygghandlingar– dokumentacja budowlana (zatwierdzona dla wykonawców)
- RH – relationshandlingar – dokumentacja powykonawcza
Dopiero otrzymanie dokumentacji o statusie BH przez wykonawcę umożliwia mu rozpoczęcie prac. Natomiast niedotrzymanie terminu przez jednostkę projektową jasno wskazuje przyczynę opóźnień całego harmonogramu. System jest brutalnie przyczynowo skutkowy, przez co prosty. Ucieczka od odpowiedzialności jest w dużym stopniu ograniczona, a osoby odpowiedzialne jasno wskazane w „łańcuchu dostaw” usług projektowych i budowlanych.
W polskich realiach. O ile mapy wraz symboliką zagospodarowania terenu i instalacji zewnętrznych są usystematyzowane, to rysunek konstrukcyjny nie. Dlaczego „tam” da się uporządkować tak prostą kwestię jak rysunek techniczny, który stanowi język komunikacji pomiędzy inżynierami i technikami, podczas gdy w naszym kraju od wielu lat panuje bezład ? Każdy na to narzeka, ale reprezentujące środowisko budowlane stowarzyszenia zawodowe, organizacje budowlane, normalizacyjne i kadr naukowe nic z tym nie robią.
Proces produkcji w zakładzie produkcji charakteryzuje się wzmożoną kontrolą jakości w stosunku do budownictwa tradycyjnego. Zarówno procesy budowlana zachodzą w jednorodnym środowisku (brak wpływów atmosferycznych) jak i poszczególne etapy podlegają kontroli „on daily basis”.
Księga Jakości systemu Zakładowej Kontroli Produkcji (ZKP) zobowiązuje do przestrzegania wytycznych europejskich norm zharmonizowanych, m.in.
- PN-EN 206+A2:2021-08 Beton - Wymagania, właściwości użytkowe, produkcja i zgodność
- PN-EN 13369:2018 - Wspólne wymagania dla prefabrykatów betonowych.
Oraz normy dedykowane poszczególnym typom prefabrykatów, np.
- PN-EN 14992:2007+A1:2012 Prefabrykaty z betonu - Elementy ścian
- PN-EN 13225:2013-09 Prefabrykaty z betonu - prętowe elementy konstrukcyjne
- PN-EN 14843:2009 Prefabrykaty z betonu - Schody, itd.
Kontroli podlegają nie tylko wyroby gotowe ale i poszczególne procesy. Każda z norm zawiera szczegółowy wykaz procesów podlegających kontroli jak i sposobu ich realizacji oraz zakresu dopuszczalnych tolerancji. Ponadto kontroli podlegają narzędzia pomiarowe, wyposażenie laboratorium, urządzenia węzła betoniarskiego, np. wagi dozowania składników betonu, a także częstotliwość badań, ocena dostawców surowców.
Jak wiadomo z praktyki budowlanej, kontrola jakości betonu wykonywana jest jedynie podczas realizacji dużych inwestycji. O ile przy realizacji inwestycji o dużym znaczeniu społeczno-gospodarczym, jak budowy tuneli, mostów czy elektrowni; można przyjąć iż kontrola ta jest prowadzona sumiennie, to przy realizacji budownictwa kubaturowego o mniejszej „randze” kontrola ta jest wyrywkowa, a sam jej przebieg często odbiega od zaleceń normowych, np. warunki przechowywania próbek sześciennych na budowie do czasu przyjazdu laborantów.
Certyfikacja zakładu produkcji wymusza stosowanie oznakowania CE wyrobów budowlanych, a co za tym idzie spełnienia wymagań ww. norm co podlega corocznemu audytowi zewnętrznej jednostki, która ma na celu weryfikację poprawności wykonania procesów.
Do ww. wymienionych procesów dochodzi jeszcze kontrola procesów bezpośrednio związanych z wytwarzaniem elementów jak np. pomiary zbrojenia czy szalunków na formie. Surowy reżim jakościowy, odpowiedni schemat organizacyjny i zbiór procedur kontrolnych drastycznie obniża ilość elementów podlegających reklamacjom.
Co więcej wyroby gotowe również podlegają kolejnej weryfikacji. Zgodnie z zapisami normowymi nie muszą być to wszystkie elementy, jednakże wprowadzenie do Księgi Jakości odpowiedniej jednostki kontrolnej i procedur weryfikacyjnych powoduje kolejne drastyczne obniżenie ilości reklamacji.
Proces jakościowy nie kończy się tylko na stricte aspektach technologicznych, ale jest jak proces ewolucji całego przedsiębiorstwa w otoczeniu biznesowym - niczym organizmów dostosowujących się do stale zmiennego środowiska naturalnego. Jakości nie da się wytworzyć tylko poprzez wypełnianie kolejnych formularzy, które z upływem czasu staną się biurokratycznym wymogiem. Jakość musi być zaszczepiona w całej organizacji firmy, gdyż geneza problemów najczęściej tkwi w źródłach nie-produkcyjnych.
Proces dążenia do jakości jest ciągły i nieskończony, a w miarę rozwoju danej firmy zatacza coraz szersze kręgi. Istnieje szereg metod mających na celu zwiększenie produktywności oraz minimalizację strat. Ich rozwój przypada na dwudziestolecie międzywojenne, a największy rozkwit przeżyły za sprawą Williama Edwarda Deminga po zakończeniu II Wojny Światowej w okupowanej przez USA Japonii oraz latach 80 XX wieku w USA. Cykl Deminga (Plan, Do, Check, Action) czy przyjęcie nowej filozofii zarządzania TQM (Total Quality Management) wpisywał się w charakterystyczną dla Japończyków filozofię kaizen, która oznaczają ciągłą poprawę zmierzającą ku doskonałości.
Proste zbiory zasad opisane w metodach 5`S, 6σ czy Lean Manufacturing brzmią chwytliwie, ale diabeł tkwi w szczegółach. Wprowadzający zmiany musi posiadać głębokie doświadczenie w znajomości procesów na wszystkich szczeblach, tzn. produkcyjnych, zarządczych, jakościowych, zakupowych, itd.
W przeciwnym wypadku zmiany okażą się nietrafione lub ugrzęzną w połowie, tworząc niepotrzebny chaos organizacyjny, a problemy jak były, tak zostaną:
Chwytliwe hasła wyglądają szczególnie dobrze na prezentacjach Power Point podczas narad z Zarządem, który oczekuje błyskawicznych oraz skokowych wzrostów wskaźników KPI. Należy jednak uzmysłowić wszystkim, iż mentalność polskiego pracownika jest diametralnie inna i nawet najlepsze wzorce nie da się skopiować wprost poprzez „ctrl+C , ctrl+V”. Filozofia ciągłego doskonalenia przegrywa tutaj z przekonaniem o własnej wyższości, a braki wiedzy i doświadczenia w stosunku do pracy sąsiednich działów wytwarzają pośród kadr efekt Krugera-Dunninga.
Efekt ten spotęgowany jest przez brak zakorzenionego poczucia odpowiedzialności w społeczeństwie. Abstrahując od „Extremalnej Odpowiedzialności” głoszonej przez byłego operatora Neavy Seals - Jocko Willinka; problem sprowadza się to do sofizmatycznych wywodów mających na celu przerzucenie przyczyny błędu na drugą osobę.
Dotyczy to pracowników poszczególnych działów i szczebli, toteż wprowadzanie zmian jest pozytywistyczną pracą u podstaw - mozolną, długotrwała jednakże nie syzyfową. Przy odpowiednio długim uporze przynosi efekty. Zmiany należy wprowadzać nie tylko poprzez procedury czy kosztowne zakupy, ale przede wszystkim od zmiany nastawienia ludzi, którzy tą pracę będą wykonywać. Dopiero po zaszczepieniu wspólnych wartości oraz wspólnej misji można realnie połączyć zarządzanie przez jakość z zarządzaniem przez cele oraz wyniki, gdyż na końcu i tak liczą się wskaźniki… $ KPI $
Autor: mgr inż. Jacek Trzcieliński