Technologie i metody budowy tuneli
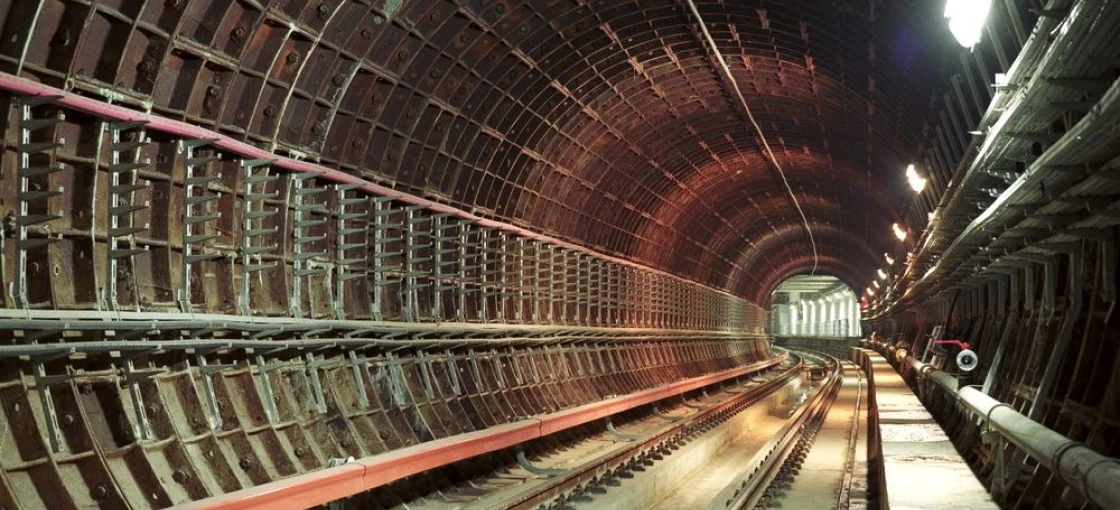
Postępująca urbanizacja spowodowała, że część ruchu komunikacyjnego zostaje przeniesiona pod ziemię. W niektórych zatłoczonych miastach budowa tunelu okazuje się jedynym rozwiązaniem problemów z przemieszczaniem. Znaczny wzrost inwestycji tunelowych przyczynia się do szukania rozwiązań gwarantujących szybki, jednocześnie bezpieczny postęp robót.
Najpopularniejszą obecnie technologią drążenia tuneli jest zastosowanie tarczy TBM (Tunnel Boring Machine). Technologia ta jest wykorzystywana z powodzeniem do wykonania tuneli drogowych, wodociągowych, kanalizacyjnych, hydroenergetycznych czy wielozadaniowych.
Drążenie tunelu – maszyny TBM
Istnieją różne rodzaje maszyn TBM, aczkolwiek działają one na podobnej zasadzie. Składają się z ogromnej tarczy, której rozmiar uzależniony jest od parametrów planowanej inwestycji. Średnica jej może wynosić od kilku do kilkunastu metrów.
Przykładowo tarcza do drążenia warszawskiego metra ma średnicę 6,3 m (co uwzględnia docelową szerokość torowiska i wysokość wagonów). Tunel pod rzeką Świną między wyspami Wolin i Uznam w Świnoujściu drążyła tarcza o średnicy 13,4 m.
Długa na kilkadziesiąt metrów maszyna TMB pozwala pomieścić w sobie wszystkie niezbędne urządzenia, takie jak agregaty prądotwórcze, pompy, systemy wentylacyjne, pomieszczenia magazynowe, a także urządzenia odpowiadające za dostarczanie elementów tunelu oraz za transport urobku.
Jak powstaje tunel w technologii TBM?
Praca maszyny polega na ruchu obrotowym tarczy, której czoło wyposażone jest w ostrza, noże oraz dyski tnące wykonane ze stali o wysokiej wytrzymałości, drążące skałę. Umieszczone są tam także dysze, które wstrzykują wodę, plastyfikatory bądź beton, służące zagęszczaniu lub zwiększeniu stopnia plastyczności gruntu, zależnie od jego rodzaju.
Jeśli zachodzi konieczność usunięcia z drogi maszyny większych kamieni, instalowana jest kruszarka, a następnie rozdrobniony materiał jest odprowadzany na powierzchnię. Można także na głowicy tarczy zainstalować odpowiednie noże, urabiające napotkane większe głazy.
W kierunku drążonej ściany tarcza przesuwana jest za pomocą siłowników hydraulicznych. Uzyskiwany w wyniku drążenia urobek gromadzony jest w komorze urobkowej, a następnie transportowany najczęściej za po mocą taśmociągu na zewnątrz.
Po wydrążeniu odpowiednio długiego odcinka odbywa się układanie obudowy tunelu. Gotowe, wykonane na odpowiedni wymiar prefabrykowane pierścienie montowane są szczelnie jeden za drugim. Przestrzeń powstająca między zewnętrzną ścianą tunelu a gruntem wypełniana jest zaprawą wiążąco-uszczelniającą. Takie działanie ma zapobiec ryzyku wystąpienia osiadań podłoża gruntowego i zapewnia poprawną współpracę pomiędzy obudową tunelu a otaczającym ją gruntem.
Praca maszyny na każdym etapie jest monitorowana przez wykwalifikowany zespół pracowników. Zbierane i analizowane na bieżąco dane pozwalają szybko zareagować na wszelkie zmiany, jak choćby występujący w danym miejscu inny rodzaj gruntu.
Drążenie tunelu a bezpieczeństwo sąsiadujących budynków
W trakcie budowy tunelu istniej ryzyko wystąpienia różnych zagrożeń, jak choćby wstrząsy sejsmiczne, osunięcia ziemi, zalania. W celu wykrycia potencjalnego niebezpieczeństwa stosuje się system monitoringu zapewniający ochronę obiektów na powierzchni. Polega na wykonaniu kilkudziesięciu tysięcy otworów sondażowych zorganizowanych w sekcje, powiązanych z oprogramowaniem pozyskującym wymiary, automatycznie przetwarzającym dane, weryfikującym pomiary, automatycznie informującym o osiągnięciu zaprogramowanych progów wymagających uwagi bądź progów alarmowych.
Ponadto w budynkach znajdujących się na powierzchni, których posadowienie i konstrukcja odbiega od współczesnych norm, umieszcza się urządzenia pomiarowe, takie jak: repery, klinometry (pochyłomierze) i pryzmaty. Obiekty znajdujące się w strefie oddziaływań tunelu, których stan zostaje uznany za niezadawalający, zabezpiecza się poprzez iniekcje gruntowe, wykonywane przed wydrążeniem tunelu. Poprzez niewielki odwiert specjalna zawiesina zostaje wtłoczona do miejsc docelowych, które mogą znajdować się na głębokości przekraczającej kilkadziesiąt metrów. Działanie to ma zapobiec osiadaniu i wychyleniu budynków. Iniekcja ma za zadanie poprawić parametry podłoża gruntowego, tworząc parasol ochronny między obszarem wiercenia tunelu a fundamentem zabezpieczanego budynku.
Zalety technologii TBM
Drążenie tuneli przy pomocy maszyn TBM obywa się przy minimalnym zakłócaniu życia mieszkańców okolic.
Technologia ta jest bardziej bezpieczna dla ludzi pracujących przy budowie tunelu, ponieważ minimalizuje ryzyko wystąpienia wypadków i zapewnia lepsze warunki pracy.
Maszyny TBM są bardziej wydajne, co pozwala na naprawdę szybkie drążenie tuneli. Wykonanie kilku cm przekopu na minutę umożliwia uzyskanie do 10 metrów postępu prac w ciągu doby.
Technologia TBM może być zastosowana w różnych, trudnych i zmiennych warunkach geologicznych.
Ta metoda jest bardziej ekonomiczna w stosunku do metod odkrywkowych. Całkowity koszt wydrążenia tunelu jest niższy, a prace zrealizowane są w znacznie krótszym czasie.
Treści powiązane
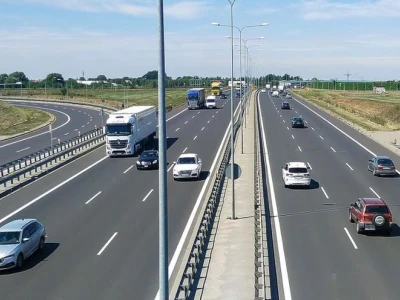
Budowa nowych dróg w Polsce w 2024 roku
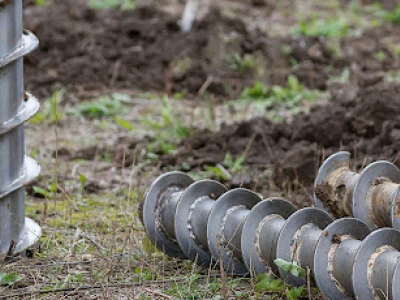
Kategorie geotechniczne gruntu i obiektów budowlanych
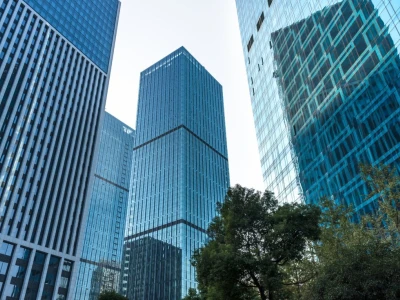
Iniekcja gruntowa – technologia stabilizacji gruntu
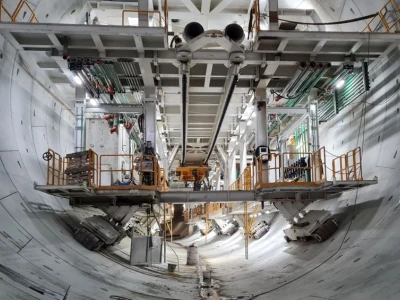
Budowa tunelu w Świnoujściu

Budowa tunelu w ciągu drogi S19
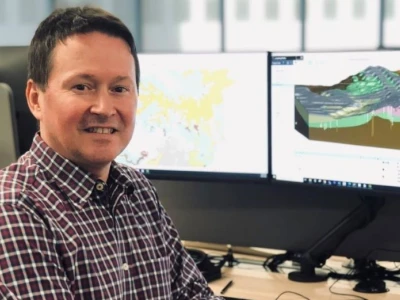