O innowacjach dla energooszczędności mówi Jakub Sąsiadek, Sales Manager PL/CZ/SK w firmie BASF
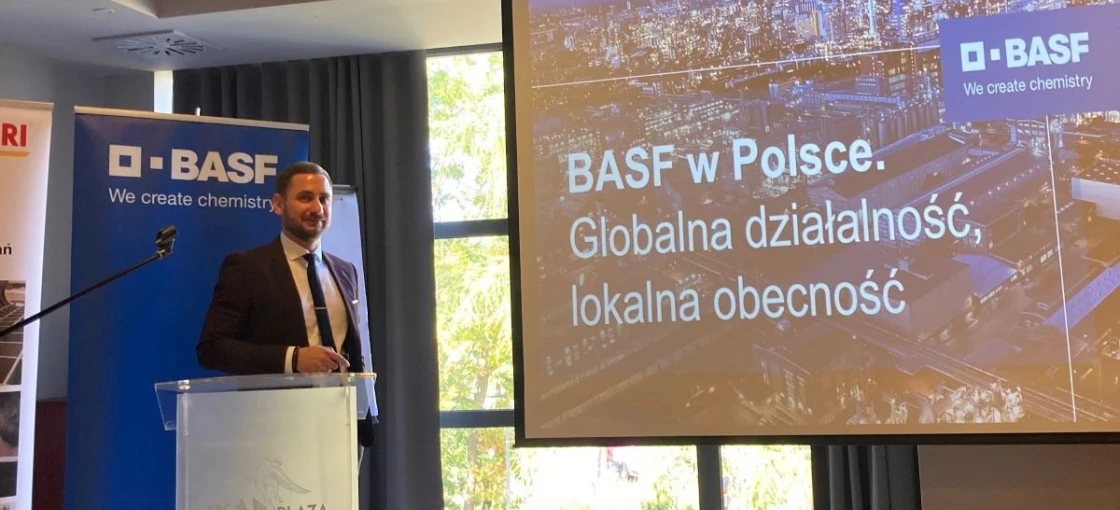
Innowacje dla energooszczędności
Firma BASF jako jeden ze swoich celów stawia sobie misję tworzenie chemii dla zrównoważonej przyszłości. Dzięki współpracy z praktycznie wszystkimi sektorami gospodarki jesteśmy w stanie wraz z klientami i partnerami wprowadzać na rynek rozwiązania odpowiadające na palące wyzwania środowiskowe.
W budownictwie mamy obecnie w ofercie wszystko to, co jest potrzebne do wytworzenia izolacji styropianowych z XPS-u oraz z poliuretanu. W portfolio BASF można znaleźć materiały oparte na nowoczesnych polistyrenach (EPS), pianach PUR i PIR. Z kolei granulaty polistyrenu do spieniania EPS-u Styropor i Neopor są stosowane do ocieplania budynków. Ponadto proponujemy ElastopirBlue – system poliuretanowy o zwiększonej odporności ogniowej i wyjątkowej izolacyjności, a także polimoczniki Elastocoat, czyli izolację wodochronną o zwiększonej odporności chemicznej, stosowaną np. jako membrana ochronna w oczyszczalniach ścieków.
Wysoka wydajność
Powyższe technologie są stale rozwijane w kierunku materiałów o coraz to wyższej wydajności, czyli de facto materiałów o jak najniższym współczynniku przewodzenia ciepła. Obecnie mamy do zaoferowania jedne z najnowocześniejszych technologii na rynku termoizolacji, jak Elastopir Blue o parametrze przewodzenia ciepła na poziome 0,019 W/(mK). W przypadku systemów poliuretanowych ważne jest stosowanie w konwencjonalnych zamkniętokomórkowych systemach izolacyjnych nowych, przyjaznych dla środowiska środków spieniających HFO. Dodatkowo pracujemy nad wyeliminowaniem uniepalniaczy halogenowych, np. halogen--free Elastopir Blue. Naszym zdaniem izolacje powinny mieć lepszą izolacyjność termiczną, odporność ogniową i nadawać się do wtórnego wykorzystania, czyli powinny być łatwiejsze w utylizacji niż te dzisiaj stosowane.
Wysokiej jakości izolacje sprzyjają zrównoważonemu rozwojowi oraz zmniejszaniu emisji CO2 w budownictwie. I tak na przykład produkty izolacyjne oparte na Neoporze wnoszą istotny wkład w realizację celów ochrony klimatu. Analiza pokazuje, że ilości Styroporu, Neoporu i Styroduru sprzedane w 2019 r. pomagały naszym klientom zaoszczędzić 62 miliony ton metrycznych emisji CO2 w całym cyklu życia tych produktów. Obliczenie to opiera się na analizie cyklu życia, która bierze pod uwagę produkcję i utylizację materiałów izolacyjnych oraz porównuje zużycie energii w odnowionym budynku z nieprzebudowywanym budynkiem przez 50 lat.
Właściciele budynków, projektanci oraz architekci nieustannie poszukują nowych rozwiązań wśród systemów i materiałów w celu tworzenia coraz to bardziej zrównoważonych oraz oszczędnych
i zielonych budynków. Ważnym aspektem dla termoizolacji budynków jest również możliwość stosowania jak najcieńszych, ale zarazem możliwie jak najbardziej wydajnych materiałów w celu zminimalizowania grubości ścian na dużych powierzchniach, a tym samym zwiększenia powierzchni użytkowej budynków.
Recycling chemiczny - drugie życie izolacji
Obecne materiały izolacyjne EPS w całości podlegają recyklingowi i mogą być ponownie wykorzystane do 100%. Natomiast BASF chce pójść o krok dalej, jako że możemy to stosować we wszystkich grupach produktowych na większą skalę ze względu na technologie tzw. recyklingu chemicznego (ChemCycling™). Posiadamy taką technologię, gdzie wszystkie tworzywa, które są zmieszane z różnych warstw, można przerobić do oleju pirolitycznego, który z kolei można zawrócić do obiegu jako jeden z surowców do produkcji nowych materiałów (także izolacyjnych). Naszym zdaniem jest to technologia przyszłości. Opierając się na recyklingu mechanicznym, czyli tradycyjnym, tylko około 20% odpadów może z powrotem trafić do ponownego przetworzenia. Dlatego nasz ChemCycling™ będzie w tej dziedzinie prawdziwym przełomem. Już dziś współpracujemy z firmami, które nam dostarczają olej pirolityczny. Wykorzystujemy go do produkcji XPS-u i do prototypowej linii Neoporu z nieoczyszczonych odpadów budowlanych. Finalnie właściwości tych produktów są takie same, ale największą zaletą jest są to, że w 100% pochodzą z recyklingu, w tym przypadku chemicznego.
Jesteśmy też jedną z pierwszych firm, która od 2022 roku ma obliczony i podany do wiadomości ślad węglowy dla wszystkich produktów. Mamy około 45 000 produktów w portfolio. Każdy z nich ma zmierzony wpływ na środowisko na każdym etapie wytworzenia. To wielkie wyzwanie, ale też jedyna słuszna droga, jeżeli chcemy w przyszłości osiągnąć neutralność klimatyczną.
Obejrzyj film:
https://www.linkedin.com/feed/update/urn:li:activi...
***
Mgr inż. Jakub Sąsiadek - Sales Manager Performance Materials Construction Poland, Czech Republic and Slovakia w firmie BASF, absolwent i wykładowca Politechniki Poznańskiej, doktorant Szkoły Doktorskiej PP, członek Wielkopolskiej Okręgowej Izby Inżynierów Budownictwa, członek Polskiego Związku Inżynierów i Techników Budownictwa.
Treści powiązane
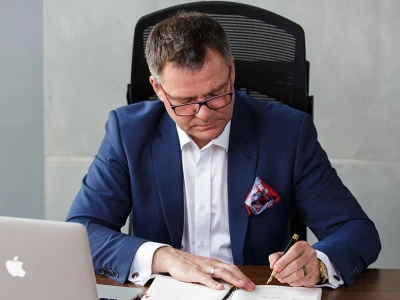
What’s up doc? - wywiad z dr inż. Krzysztofem Poganem, właścicielem firmy KP-Project
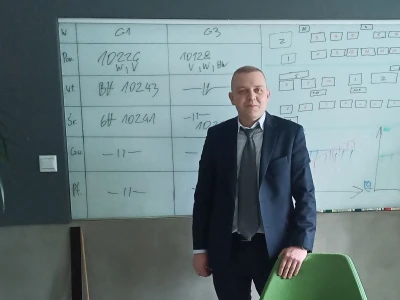
Planowanie produkcji oraz proces produkcji - komentuje Jacek "Prefabrykator" Trzcieliński
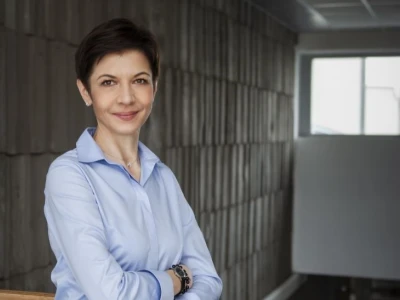
Czy odpad może być cennym składnikiem betonu? - dr hab. inż. Magdalena Dobiszewska, prof. PBŚ
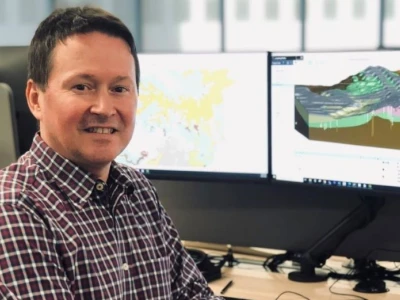
Budowa metra w Sydney okiem geotechnika - wyjaśnia inżynier Robert Dawidowicz
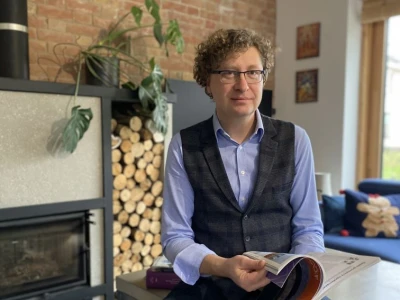
Wszystkie kolory betonu – wywiad z mgr. inż. Krzysztofem Kuniczukiem, właścicielem firmy Technologia Betonów Architektonicznych i Specjalistycznych
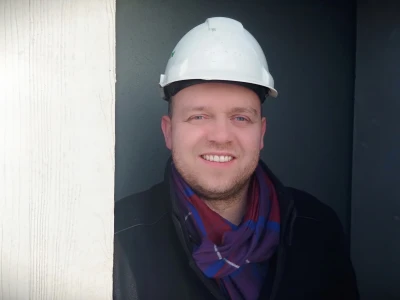
Prefabrykaty - fakty i praktyka. Planowanie inwestycji i proces projektowy - komentuje inż. Jacek Trzcieliński
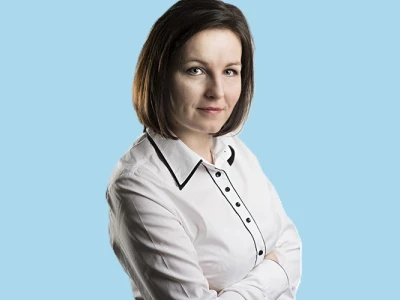
Standard klasyfikacji emisyjności betonu towarowego - komentuje dr inż. Grażyna Bundyra-Oracz
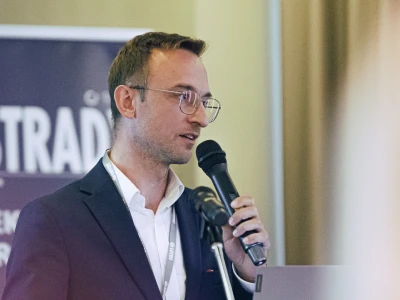
O działalności Polskiego Związku Producentów Kruszyw i rynku kruszyw opowiada dr inż. Łukasz Machniak
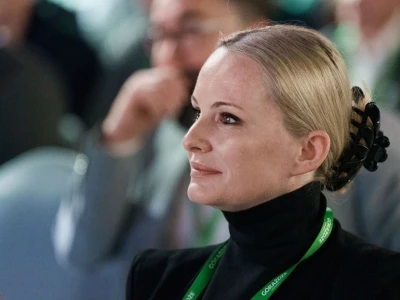
Zdrowa Architektura Zrównoważona - komentarz dr inż. arch. Marty Promińskiej
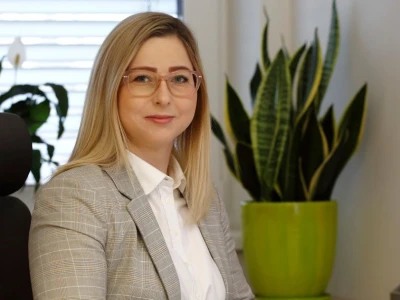